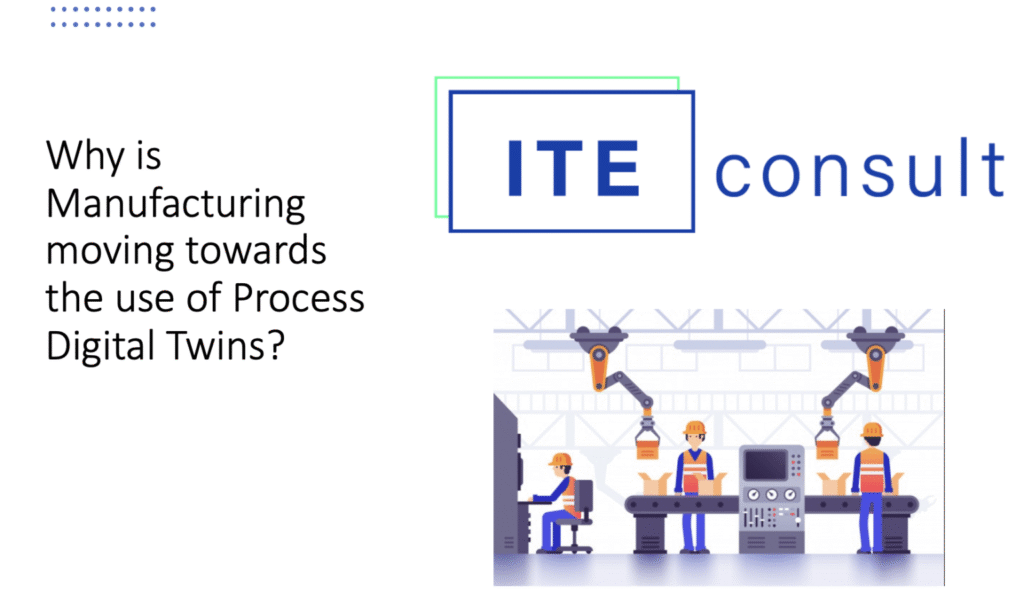
Why is it manufacturing moving towards the use of process digital twins? Initially, it was all about product digital twin, a simulation model of how to produce the product itself.
But collaboration across the entire virtual environment is required to optimize the whole process. A process digital twin looks at the process beyond a single machine or working station, it relates and plays in the entire production environment.
A digital twin is a simulation model. A place where you get the answers you need for an accurate planning. When running a process digital twin, you get insights of your process, so you are able to take better informed decisions and it also delivers an optimized plan or schedule for the data flow you are using as input. Both types of outputs are of great value.
Today combining Data with algorithms and the information of each workstation or production step, you can build a virtual replica of what is happening in the entire factory. Which are the benefits?
First quick answer to this question,
Running the most probable scenarios for your future production according to the most probable demands, will deliver you an optimized plan.
But how am I sure that that the tool has considered all the constrains and specific situations that may happen on the entire factory?
What if the problem is labor, or delays in raw material delivery or we must repair a Line? And so many other unpredictable situations!
Process Digital twins are not black boxes, you can follow and inspect each step of the process and understand what is happening, when and where are your bottlenecks appearing running it in an analytical way, when you want deeper insights of relations between processes. When you run it as an optimizer, you define goals, and the tools delivers the optimal plan.
The benefits of a process digital twins is that you run your model with all the possible scenarios you expect or imagine and you get your optimized plans in matter of minutes and when the unpredictable arrives, you just re-run your model for that specific scenario and in minutes you have a new optimal plan. Unpredictable will be easier to deal with.
Just one tip or two from our experience in building process simulations.
There are different approaches when building a model, and it may feel it is a huge development, but it isn´t.
A recommended approach, once you have framed your process and defined which are your variable inputs and which are your fixed inputs (those that no action on your side will change them), will be doing a quick set up of the model.
Today building a process digital twin is done by setting up auto/programmatic data collection from external sources (e.g., SAP) then based on those inputs built a simulation model to operate against those inputs and plugged the simulations directly into a solver to generate optimal solutions, customizing for the user different input scenarios. This approach allows companies to have their process digital twins integrated with data and up and running in shorter times.
Hope you find this article of some help, we will go deeper into process digital twins development in further articles.