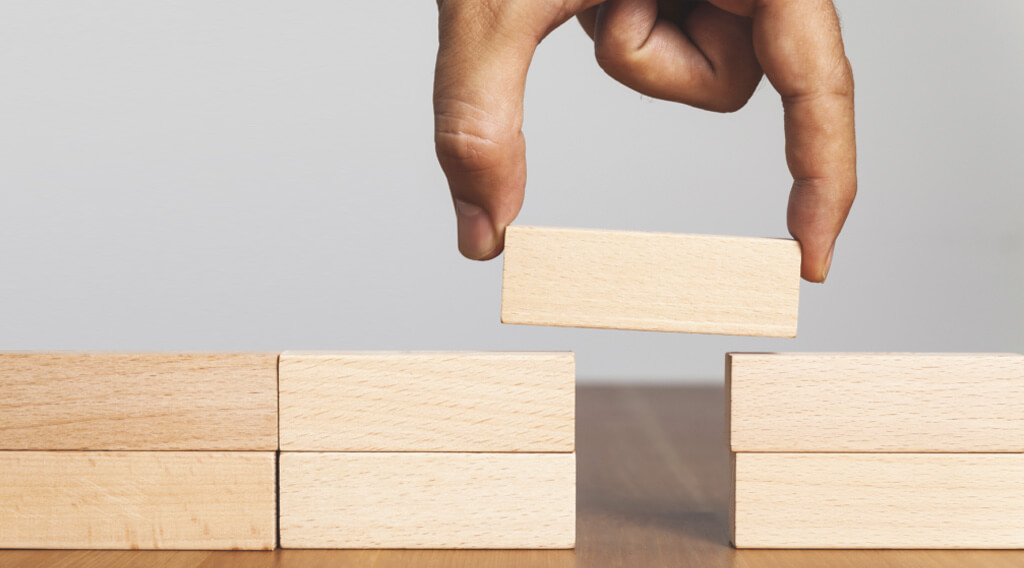
It is crucial to clearly establish the planning parameters that will guide both tactical planning and scheduling. These parameters encompass various factors, including production capacity, lead times, resource availability, and any applicable constraints.
Utilizing software tools that allow for running “what if” scenarios at both levels, using the same parameters but on a different scale, ensures the integration of the detailed schedule with the master plan.
These tools should be used frequently to continuously align the plan with real-time data, especially in the face of disruptions to the schedule.
Regarding how a Process Digital Twin Solution works:
üThe solution begins by proposing long-term plans (12-18 months) based on forecasted demand for different scenarios. This involves considering factors such as production capacity, lead times, resource availability, and relevant constraints. It is important to optimize the plan by finding trade-offs between process steps.
üOnce the long-term plan is in place, a simulation is performed for the short term (6 weeks to 3 months). This simulation incorporates detailed information specific to each product, moving away from average values. Achieving this level of detail, simulating real-time production on a second-by-second basis, can only be accomplished using a digital twin. The resulting detailed schedule is then merged with the master plan, aligning the weekly planning schedule and resolving it within minutes.
üSimulating the process flow is the most effective way to anticipate and make informed decisions. It reduces time, waste, inventory, and helps meet deadlines, among other benefits. It is a sustainable tool for a sustainable world!
üWhen implementing a simulation tool, it is important to consider the inclusion of all relevant parameters during the onboarding process. The development and implementation of such a solution should be swift, allowing it to be up and running in a short period of time.